ElectricalLY-HEATED RTO
Very High VOC Elimination
with High Thermal Efficiency
Tecam’s Electrically-heated RTO
Due to the current world situation, energy transition and taking into account the European Union objectives, recently there has been a shift in the demand of how companies want to heat up the oxidation chambers of their Regenerative Thermal Oxidizer (RTO) systems for Volatile Organic Compounds (VOC) emissions removal at their production plants.
The trend has gone from burner-powered to electric-powered or to other forms of power, therefore flameless, and therefore without any NOX emissions derived from the burner, for a greener output.
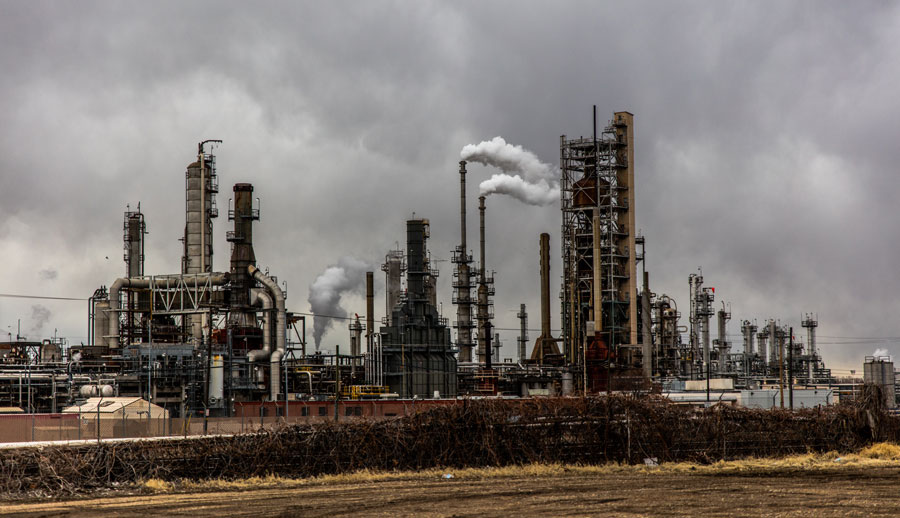

Tecam’s tailor-made design
You can always count on tailor-made solutions with Tecam and, where necessary, the development of specific components, software and/or materials. Our technicians engage with every project, using their expertise and knowledge to design customised equipment for each case and customer.
No matter how big or complex the problem, Tecam is the technology partner that will provide you with the solutions you need at all times.
The advantages of Tecam Electrically-heated RTO equipment
- Very High VOC elimination.
- High thermal efficiency.
- Once it reaches operating temperature, the system runs on auto thermal mode, with zero electricity consumption.
- No flame and therefore no NOx associated to combustion.
- Reduction of CO2 emissions, zero if renewable energy is used.
- Equal features and performance as Tecam conventional RTOs.
- Less noise around the equipment, due to the lack of a burner fan.
- Easier to do the installation and commissioning.
- Low operating costs.
- Simple and robust design.
- Almost no maintenance required.

Contact us
How Electrically-heated RTO technology works
RTO equipment usually works with burners that use gas or fuel to heat up the oxidation chamber during start-up so that oxidation of VOCs can take place.
In the case of flameless RTOs, there is no burner and therefore no flame and no NOX emissions generated. The oxidation chamber gets heated up via some electrical resistances placed inside.
- During start-up -> the electric resistances will work at 100 % to be able to heat the RTO oxidation chamber up to the required temperature (eg. 850 ºC, 1100 ºC).
- During operation -> the consumption of electricity will depend on the VOC concentration at the inlet and its calorific value. If the concentration is above the autothermal point, resistances will turn off. Otherwise, if the concentration is lower than this point, the thyristors will modulate the resistances power to maintain the oxidation chamber temperature at the required temperature (eg. 850 ºC, 1100 ºC) to guarantee the oxidation of VOCs.
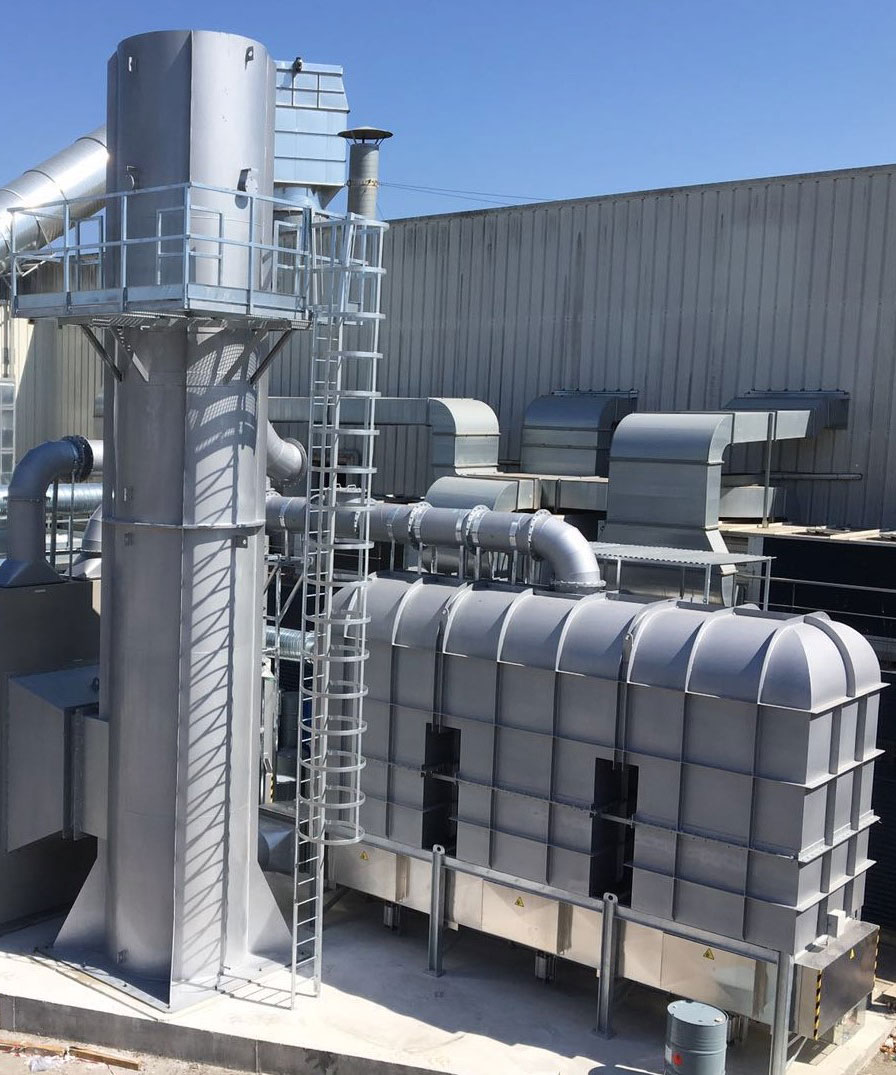
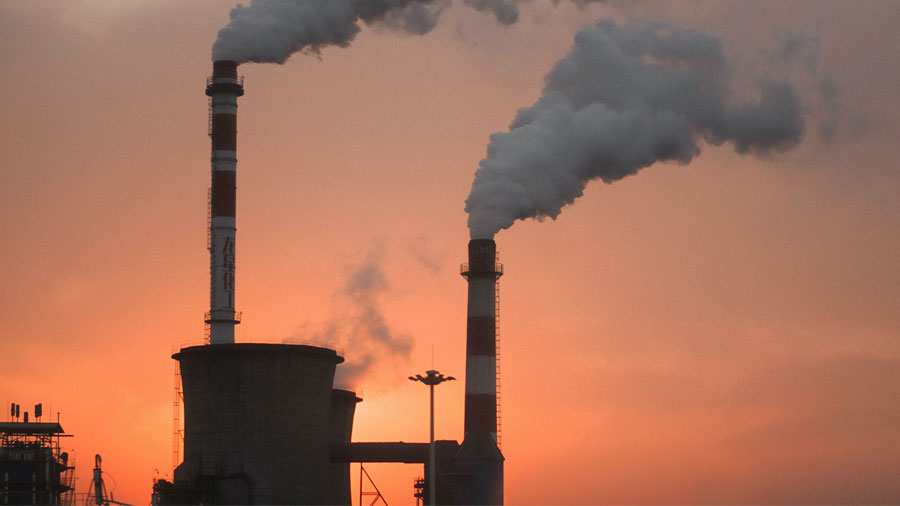
The ideal solution for eliminating VOCs in gaseous emissions, suitable for almost every industrial sector
Electrical RTO technology is suitable for all kinds of solvent concentrations, from low to medium and high, as well as indicated for installation in sectors and applications such as chemical, coating, flexoprinting, odour control, etc.
Specialists in the sectors that are most sensitive to environmental impacts
We drive sustainable productivity and innovation for industries with more extensive and more complex needs.
Related news
VOC emissions generated from wastewater treatment basins in refineries and petrochemical plants – how to treat them
The challenge Wastewater treatment basins represent a major challenge at an environmental level, since they emit Volatile Organic Compounds (VOC) emissions and generate odours due to the degradation of organic matter, which affect both people working at the plant, as...
Exhaust emissions and waste treatment in the Petrochemical sector
The petrochemical industry, and each refinery in particular, is unique and different in terms of process integration and the origin of raw materials. In that sense, you need to find an environmental expert who can provide you with customised environmental technology...
VOC concentrators + RTO, the perfect solution for Automotive emissions treatment
When it comes to environmental issues, there are specific aspects related to the Automotive sector that we have to consider. During automotive production, there are different processes that generate gas emissions, liquid discharges and solid and semi-solid...